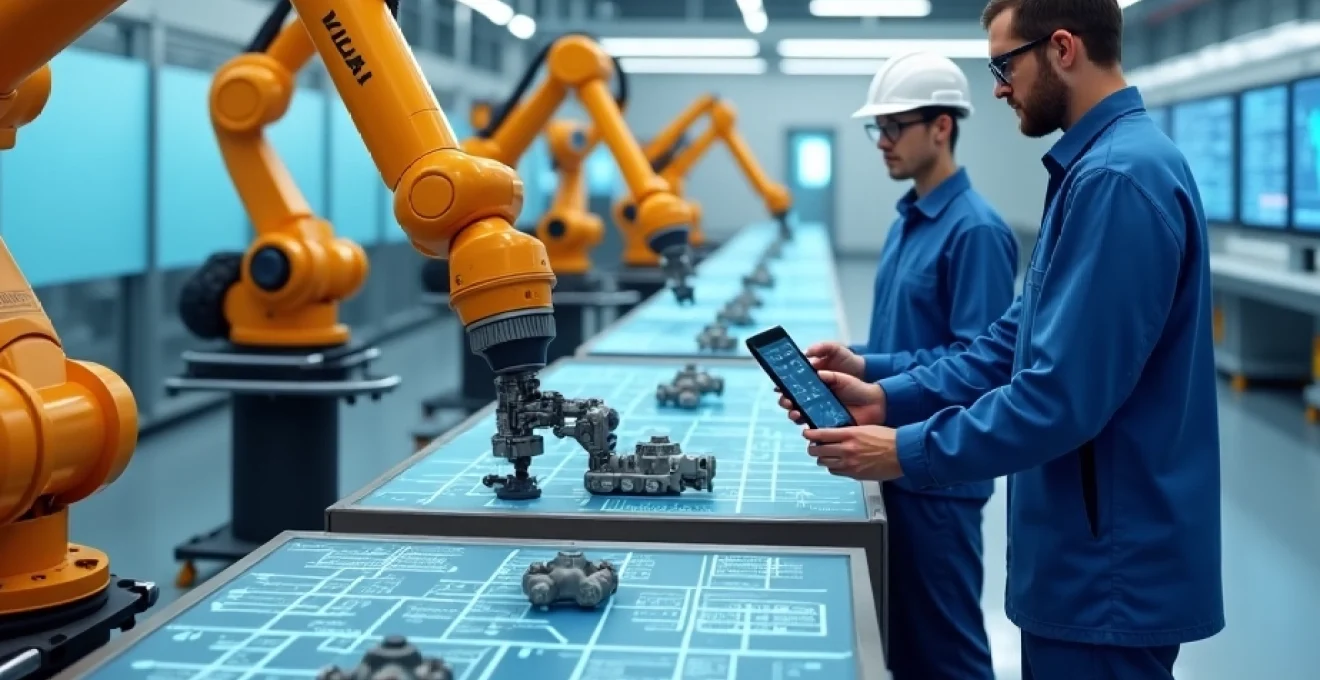
La robótica avanzada representa la vanguardia tecnológica en la transformación digital del sector manufacturero. A diferencia de los sistemas automatizados convencionales, los robots industriales modernos incorporan capacidades de percepción, toma de decisiones autónomas y adaptabilidad que revolucionan los procesos productivos. Esta evolución está redefiniendo completamente los parámetros de eficiencia, precisión y flexibilidad en entornos industriales que antes parecían haber alcanzado sus límites operativos.
El mercado global de robótica industrial crece a un ritmo anual del 13,5%, impulsado por la demanda de soluciones que combinen la potencia mecánica con sistemas de inteligencia artificial cada vez más sofisticados. Las estadísticas más recientes indican que se alcanzará un volumen de mercado superior a los 89.100 millones de dólares para 2026, convirtiéndose en uno de los pilares fundamentales de la cuarta revolución industrial.
La integración de sensores avanzados, algoritmos de aprendizaje automático y arquitecturas de control distribuido permite a estos sistemas realizar tareas complejas que antes requerían intervención humana constante. Esta convergencia tecnológica no solo maximiza la productividad, sino que también mejora la seguridad laboral y optimiza el consumo energético en las instalaciones industriales modernas.
Fundamentos de la robótica industrial avanzada
La robótica industrial avanzada se fundamenta en la confluencia de diversos campos tecnológicos que trabajan en armonía para crear sistemas autónomos capaces de realizar tareas complejas. El núcleo de estos sistemas comprende elementos mecánicos de precisión, electrónica de control avanzada, software especializado y algoritmos de inteligencia artificial que permiten la toma de decisiones contextuales. Esta combinación multidisciplinar representa un salto cualitativo respecto a la automatización convencional.
Los robots industriales modernos se caracterizan por su capacidad para procesar información en tiempo real, adaptarse a cambios en su entorno y ejecutar operaciones con una precisión submilimétrica. Según datos recientes, la precisión posicional de los robots industriales de última generación alcanza valores de ±0,02 mm, lo que permite aplicaciones en micromontaje y fabricación de componentes electrónicos ultraprecisos.
La arquitectura funcional de estos sistemas incluye múltiples capas operativas: desde los actuadores y sensores físicos hasta los sistemas de control de alto nivel basados en modelos predictivos. La integración de estas capas requiere protocolos de comunicación industrial avanzados como EtherCAT, Profinet o OPC UA, que garantizan la sincronización y el intercambio de datos con latencias inferiores a un milisegundo.
Arquitectura de sistemas robóticos kuka y fanuc
Los sistemas robóticos de fabricantes líderes como Kuka y Fanuc representan el estado del arte en arquitecturas de automatización industrial. Estos robots se estructuran en torno a un diseño modular que integra controladores centralizados, servomotores de alta dinámica y sensores distribuidos. La arquitectura Kuka KR C5 implementa un enfoque de control multicapa que separa las funciones de planificación de movimiento de la ejecución en tiempo real, permitiendo recalcular trayectorias en microsegundos.
Fanuc, por su parte, ha desarrollado la plataforma R-30iB Plus con capacidades de procesamiento paralelo que gestiona simultáneamente hasta 128 ejes de movimiento coordinado. Este sistema implementa el concepto de Motion Cell Controller
, donde cada unidad robótica puede funcionar de manera autónoma o como parte de un sistema distribuido mayor, intercambiando información con otros robots mediante protocolos de comunicación industrial avanzados.
La integración de unidades de procesamiento dedicadas para visión artificial y análisis sensorial permite a estos sistemas procesar grandes volúmenes de datos sin afectar a las funciones de control de movimiento. Esta separación de responsabilidades computacionales garantiza tiempos de respuesta deterministas incluso en entornos altamente dinámicos.
Mecatrónica aplicada en robots articulados de seis ejes
Los robots articulados de seis ejes representan el paradigma dominante en la automatización industrial flexible. Su diseño mecatrónico integra motores de alta densidad de potencia, reductores armónicos con backlash próximo a cero y encoders de alta resolución. Esta combinación permite movimientos fluidos con aceleraciones superiores a 8G manteniendo precisiones posicionales submilimétricas incluso en operaciones de alta velocidad.
El diseño estructural de estos robots emplea materiales compuestos y aleaciones ligeras que optimizan la relación resistencia-peso. Los robots de última generación incorporan técnicas de compensación dinámica que corrigen en tiempo real las desviaciones causadas por efectos inerciales, flexiones estructurales o dilataciones térmicas. Estas correcciones se aplican mediante algoritmos adaptables que ajustan los parámetros del modelo dinámico según las condiciones operativas.
La transmisión de potencia en cada articulación utiliza tecnologías de accionamiento directo o reductores cíclicos con eficiencias superiores al 95%. Los sistemas de refrigeración integrados permiten ciclos de trabajo continuos incluso en aplicaciones de alta carga, manteniendo las temperaturas operativas dentro de rangos óptimos para maximizar la vida útil de los componentes.
Sistemas de control distribuido en entornos IIoT
La integración de robots industriales en entornos IIoT (Industrial Internet of Things) ha revolucionado los paradigmas de control tradicionales. Los sistemas modernos implementan arquitecturas distribuidas donde las funciones de control se reparten entre múltiples nodos computacionales comunicados mediante redes industriales de alto rendimiento. Esta descentralización mejora la resiliencia del sistema, permite escalabilidad y facilita la implementación de estrategias de mantenimiento predictivo.
Las plataformas IIoT modernas gestionan entre 100.000 y 500.000 puntos de datos por segundo provenientes de toda la infraestructura robótica. Estos datos se procesan mediante algoritmia avanzada para detectar patrones, predecir fallos y optimizar parámetros operativos. La implementación de protocolos como OPC UA TSN (Time Sensitive Networking) garantiza comunicaciones deterministas con jitter inferior a 100 microsegundos.
El edge computing juega un papel fundamental en estos entornos, procesando datos críticos en tiempo real cerca de su origen antes de transmitir información agregada a sistemas de nivel superior. Esta jerarquización del procesamiento permite reducir latencias en lazos de control críticos mientras se mantiene la capacidad de análisis global del sistema productivo.
Algoritmos de planificación de trayectorias y evitación de colisiones
Los robots industriales avanzados implementan algoritmos sofisticados para la planificación de movimientos y la evitación dinámica de colisiones. Técnicas como RRT* (Rapidly-exploring Random Tree) y CHOMP (Covariant Hamiltonian Optimization for Motion Planning) permiten generar trayectorias óptimas incluso en entornos complejos y cambiantes. Estos algoritmos evalúan miles de posibles rutas en milisegundos para seleccionar aquellas que minimicen tiempo, energía o desgaste.
La evitación de colisiones en tiempo real se implementa mediante una combinación de sensores externos (escáneres láser, sistemas de visión) y modelos virtuales del entorno. Los algoritmos de detección de colisiones utilizan representaciones geométricas optimizadas como Oriented Bounding Boxes
o Swept Sphere Volumes
que permiten cálculos rápidos de distancias mínimas entre objetos en movimiento.
Las versiones más avanzadas de estos sistemas utilizan algoritmos predictivos que anticipan el movimiento de objetos dinámicos y recalculan trayectorias con antelación. Esta capacidad predictiva resulta esencial en entornos colaborativos donde robots y humanos comparten espacio de trabajo, permitiendo movimientos fluidos que respetan distancias de seguridad dinámicas.
Tecnologías de percepción en robots industriales
La capacidad perceptiva representa uno de los avances más significativos en la robótica industrial moderna. Los sistemas actuales incorporan múltiples modalidades sensoriales que les permiten construir representaciones precisas de su entorno e interactuar con él de manera adaptativa. Esta percepción multimodal transforma robots programados en sistemas conscientes de su contexto operativo, capaces de responder a variaciones y eventos imprevistos.
Según estudios recientes, la incorporación de tecnologías avanzadas de percepción en entornos industriales reduce los tiempos de inactividad no planificados hasta en un 45% y aumenta la flexibilidad productiva en un 37%. Estos datos reflejan el impacto transformador que estos sistemas tienen en la operativa industrial contemporánea.
La percepción robótica no es simplemente la adquisición de datos sensoriales, sino la capacidad de extraer información significativa del entorno para tomar decisiones contextuales en tiempo real.
Los sensores actuales generan volúmenes masivos de datos que deben procesarse con algoritmos especializados para extraer información relevante. Un sistema robótico industrial típico equipado con visión 3D, sensores táctiles y monitorización de parámetros dinámicos procesa más de 250 MB de datos por segundo, requiriendo arquitecturas computacionales optimizadas para aplicaciones en tiempo real.
Sistemas de visión artificial 3D con cámaras basler
Los sistemas de visión artificial 3D representan uno de los avances más significativos en la percepción robótica industrial. Las cámaras Basler de alta velocidad, con tasas de adquisición superiores a 120 fps y resoluciones que superan los 12 MP, se combinan con técnicas de iluminación estructurada, estereoscopía o tiempo de vuelo para generar nubes de puntos tridimensionales con precisiones submilimétricas.
El procesamiento de estas nubes de puntos se realiza mediante algoritmos especializados como RANSAC para detección de planos, ICP para registro de superficies o filtros de Kalman para seguimiento de objetos. Las GPU industriales aceleran estos cálculos, permitiendo procesar más de 10 millones de puntos por segundo y extraer características geométricas en tiempo real.
Las aplicaciones más avanzadas integran deep learning para el reconocimiento y clasificación de objetos incluso en condiciones adversas como iluminación variable, oclusiones parciales o posturas aleatorias. Redes neuronales convolucionales especializadas como PointNet++ logran precisiones de clasificación superiores al 98% incluso con objetos nunca vistos previamente durante el entrenamiento.
Procesamiento de datos LIDAR para navegación autónoma
Los sistemas LIDAR (Light Detection and Ranging) han revolucionado la navegación autónoma de robots industriales móviles. Estos sensores generan nubes de puntos tridimensionales con alcances de hasta 200 metros y precisiones centimétricas, permitiendo a los robots construir mapas detallados de su entorno y localizarse con exactitud incluso en espacios dinámicos.
El procesamiento de datos LIDAR se fundamenta en algoritmos como NDT (Normal Distributions Transform) o LOAM (LIDAR Odometry and Mapping) que permiten el registro de escaneos consecutivos y la construcción de mapas globales consistentes. Estas técnicas logran precisiones de localización inferiores a 2 cm incluso después de recorridos de varios kilómetros.
La segmentación semántica de nubes de puntos LIDAR permite identificar y clasificar elementos del entorno como personas, maquinaria, estanterías o zonas de tránsito. Esta comprensión contextual resulta esencial para la planificación de rutas seguras y eficientes en entornos industriales complejos, donde los robots deben navegar respetando normativas de seguridad y priorizando flujos de trabajo específicos.
Sensores táctiles y hápticos en manipulación de precisión
La manipulación robótica avanzada se beneficia enormemente de la integración de sensores táctiles y hápticos que proporcionan información sobre fuerzas, presiones y texturas durante la interacción con objetos. Las matrices táctiles modernas incorporan entre 1.000 y 10.000 elementos sensibles distribuidos en superficies conformables que se adaptan a la geometría de los efectores finales.
Estos sensores permiten implementar estrategias de control por impedancia o admitancia, donde el robot regula dinámicamente su rigidez en función de las fuerzas detectadas. Esta adaptabilidad resulta crucial en aplicaciones de montaje de precisión, donde tolerancias de pocas micras requieren una interacción delicada y controlada con las piezas.
Las tecnologías más recientes incluyen sensores bioinspirados que emulan la estructura de la piel humana, con múltiples capas sensibles a diferentes modalidades: presión, vibración, temperatura y proximidad. Estos sistemas multimodales generan representaciones ricas de la interacción física que permiten manipular objetos frágiles o deformables con una destreza previamente inalcanzable para sistemas robóticos industriales.
Fusión de sensores multimodales para entornos complejos
Los entornos industriales complejos requieren la integración de múltiples modalidades sensoriales para construir representaciones robustas y completas. La fusión sensorial combina datos de visión, LIDAR, sensores inerciales, táctiles y acústicos mediante técnicas probabilísticas como filtros de partículas o redes bayesianas dinámicas que modelan explícitamente las incertidumbres asociadas a cada sensor.
Esta integración multimodal permite superar las limitaciones inherentes a cada tipo de sensor: la visión puede verse afectada por condiciones de iluminación, los sensores táctiles solo proporcionan información local, y los sistemas LIDAR pueden tener dificultades con materiales transparentes o altamente reflectantes. La combinación sinérgica de estas modalidades genera sistemas perceptivos más robustos y adaptables.
Los algoritmos de fusión sensorial más avanzados implementan arquitecturas atencionales que priorizan dinámicamente diferentes fuentes de información según el contexto y la tarea. Esta capacidad para focalizar recursos computacionales en las señales más relevantes en cada momento permite optimizar el rendimiento del sistema mientras se mantienen tiempos de respuesta compatibles con operación en tiempo real.
Robótica colaborativa (cobots) en líneas de producción
La robótica colaborativa representa un paradigma revolucionario que redefine la interacción entre humanos y máquinas en entornos industriales. Los cobots, diseñados específicamente para trabajar junto a operarios sin barreras físicas, combinan la flexibilidad y capacidad cognitiva humana con la precisión y resistencia de los sistemas robóticos. Esta simbiosis operativa está transformando radicalmente los modelos productivos tradicionales.
El mercado global de robots colaborativos crece a un ritmo anual del 25%, superando las proyecciones iniciales de la industria. En 2023, según datos de la International Federation of Robotics, se instalaron más de 35.000 unidades colaborativas en todo el mundo, representando ya el 8% del mercado total de robótica industrial. Esta aceleración demuestra la creciente aceptación de estos sistemas en entornos productivos tradicionalmente reacios a la automatización completa.
La integración de cobots en líneas de producción está generando retornos de inversión promedio entre 8 y 12 meses, significativamente menores que los 18-24 meses habituales en robótica industrial convencional. Esta eficiencia económica, combinada con su flexibilidad operativa, los convierte en la solución preferida para PYMES que inician su transición hacia la Industria 4.0.
Arquitectura de seguridad ISO/TS 15066 en robots universal robots
La seguridad representa el pilar fundamental en el diseño de robots colaborativos. Universal Robots ha implementado una arquitectura de seguridad multicapa conforme a la especificación técnica ISO/TS 15066, que establece los requisitos específicos para espacios de trabajo donde humanos y robots interactúan simultáneamente. Esta normativa clasifica cuatro modelos de operación colaborativa: parada de seguridad monitorizada, guiado manual, monitorización de velocidad y separación, y limitación de potencia y fuerza.
Los cobots UR incorporan sensores redundantes que monitorizan continuamente parámetros críticos como fuerza, velocidad y posición en cada articulación. El controlador de seguridad dedicado procesa estos datos a 500 Hz, garantizando tiempos de respuesta inferiores a 2 ms ante detección de anomalías. Esta arquitectura implementa el concepto de Safety-Rated Monitored Stop
, que detiene inmediatamente el movimiento cuando un humano entra en zonas predefinidas del espacio operativo.
La limitación de potencia y fuerza se consigue mediante un diseño mecánico optimizado con transmisiones de baja inercia y algoritmos adaptativos que ajustan dinámicamente los límites de energía transferible en función de la herramienta montada y la tarea ejecutada. Las pruebas de validación confirman que estos sistemas mantienen fuerzas de impacto por debajo de los umbrales de dolor establecidos en estudios biomecánicos (140 N para impactos transitorios y 80 N para compresiones sostenidas).
Implementación de ABB YuMi en ensamblaje de precisión
El robot colaborativo YuMi de ABB representa un referente en aplicaciones de ensamblaje de precisión, especialmente en electrónica de consumo e instrumentación médica. Su diseño de doble brazo con 14 grados de libertad y capacidad de carga de 500 gramos por brazo permite replicar movimientos bimanuales humanos manteniendo precisiones de posicionamiento de ±0,02 mm incluso a velocidades operativas de 1500 mm/s.
La implementación de YuMi en líneas de ensamblaje de dispositivos electrónicos ha demostrado aumentos de productividad del 27% y reducciones del 84% en tasas de defectos comparado con operaciones manuales. Su capacidad para manipular componentes frágiles como microprocesadores o conectores miniaturizados se fundamenta en pinzas servo-controladas con retroalimentación de fuerza integrada que aplica presiones tan precisas como 0,1 N.
Los casos de éxito documentados incluyen fabricantes de audífonos que utilizan YuMi para ensamblar componentes con tolerancias inferiores a 50 micras, o productores de relojes suizos que implementan células robotizadas para operaciones de precisión anteriormente realizadas exclusivamente por artesanos especializados. La flexibilidad del sistema permite reconfiguraciones rápidas para diferentes variantes de producto, un aspecto crucial en mercados con ciclos de vida cada vez más cortos.
Programación intuitiva mediante demostración física
Una de las características diferenciales de los robots colaborativos es su capacidad para ser programados mediante demostración física, eliminando la necesidad de conocimientos especializados en lenguajes de programación robótica. Esta modalidad de enseñanza, conocida como Programming by Demonstration (PbD), permite a operarios sin formación técnica avanzada configurar nuevas tareas en cuestión de minutos en lugar de horas.
El proceso se fundamenta en sistemas de guiado manual donde el operario mueve físicamente el brazo robótico a través de las posiciones deseadas mientras el sistema registra trayectorias, puntos clave y fuerzas aplicadas. Algoritmos de aprendizaje procesan estos datos para generar programas optimizados que reproducen la intención del usuario mejorando aspectos como suavidad de movimiento, consumo energético y tiempo de ciclo.
Las interfaces gráficas táctiles complementan este enfoque, permitiendo ajustes precisos y programación de lógicas condicionales mediante diagramas de flujo visuales. Estudios recientes indican que este paradigma de programación reduce el tiempo de configuración en un 85% y disminuye el coste de entrenamiento de personal en un 73% comparado con métodos tradicionales de programación textual, factores críticos para manufacturas con alta variabilidad de producto.
Integración de cobots kawasaki con operarios humanos
Kawasaki ha desarrollado una nueva generación de robots colaborativos que profundiza en la simbiosis operativa entre humanos y máquinas. Su plataforma duAro, con configuración SCARA de doble brazo montada sobre base móvil, implementa un sistema de «control cooperativo» donde humano y robot pueden manipular simultáneamente la misma pieza, combinando la precisión mecánica con la capacidad de adaptación humana.
La integración efectiva se fundamenta en interfaces multisensoriales que incluyen retroalimentación háptica bidireccional, permitiendo al operario «sentir» las fuerzas experimentadas por el robot. Esto resulta particularmente valioso en operaciones de acabado superficial donde se requiere adaptar la presión según variaciones en el material. Los sistemas de seguimiento de movimiento mediante cámaras de profundidad complementan esta interacción, permitiendo al robot anticipar intenciones del operario y adaptar su comportamiento en tiempo real.
Análisis ergonómicos demuestran que esta colaboración reduce la carga biomecánica sobre operarios en un 63% para tareas repetitivas, mientras aumenta la precisión en un 42% comparado con operaciones exclusivamente manuales. El modelo «asistente robótico» implementado por Kawasaki aumenta la productividad mientras preserva la capacidad humana para tomar decisiones contextuales complejas, creando un equilibrio óptimo entre automatización y flexibilidad operativa.
Inteligencia artificial aplicada a la robótica industrial
La convergencia entre inteligencia artificial y robótica industrial representa uno de los avances más transformadores en automatización avanzada. Esta sinergia tecnológica dota a los sistemas robóticos de capacidades cognitivas que trascienden la programación determinista tradicional, permitiéndoles aprender de la experiencia, adaptarse a situaciones imprevistas y optimizar continuamente su rendimiento sin intervención humana explícita.
Según análisis de McKinsey, la implementación de sistemas robóticos potenciados con IA genera incrementos de productividad entre el 30% y 70% en entornos industriales, dependiendo del sector y aplicación específica. Las capacidades de auto-optimización reducen los tiempos de inactividad no planificados en un 45% y disminuyen el consumo energético hasta en un 25% mediante ajustes dinámicos de parámetros operativos.
La robótica industrial impulsada por IA no simplemente automatiza tareas predefinidas, sino que continuamente descubre nuevas formas de mejorar procesos que los propios ingenieros humanos no habrían identificado.
La progresión desde sistemas programados hacia robots que aprenden autónomamente está transformando fundamentalmente las metodologías de implementación industrial. Las soluciones más avanzadas combinan conocimiento experto codificado con capacidades de aprendizaje que permiten adaptar este conocimiento a las condiciones específicas de cada instalación, creando sistemas que mejoran constantemente con cada hora de operación.
Aprendizaje por refuerzo en optimización de procesos FANUC
FANUC ha implementado arquitecturas de aprendizaje por refuerzo (RL) que permiten a sus robots optimizar procesos industriales complejos mediante experimentación guiada. Estos sistemas definen funciones de recompensa basadas en métricas como tiempo de ciclo, calidad del producto o consumo energético, y permiten al robot explorar variaciones en parámetros operativos para maximizar el rendimiento global.
La plataforma FANUC FIELD system integra algoritmos RL como Proximal Policy Optimization (PPO) y Soft Actor-Critic (SAC) que gestionan el equilibrio entre exploración de nuevas estrategias y explotación del conocimiento adquirido. Los espacios de estados en aplicaciones industriales típicas comprenden entre 20 y 100 dimensiones, con espacios de acción continuos que requieren arquitecturas de redes neuronales profundas con normalización por capas para estabilizar el entrenamiento.
Un caso paradigmático es la optimización de procesos de desbarbado en fundición de aluminio, donde variables como velocidad de avance, presión aplicada y orientación de herramienta interactúan de manera compleja. Los sistemas FANUC con RL logran reducir tiempos de ciclo en un 24% mientras disminuyen el desgaste de herramientas en un 38% comparado con parámetros definidos por expertos humanos, demostrando capacidad para descubrir estrategias contra-intuitivas pero altamente efectivas.
Redes neuronales convolucionales para clasificación de piezas
La implementación de redes neuronales convolucionales (CNN) ha revolucionado las capacidades de inspección visual y clasificación de componentes en líneas robotizadas. Estos sistemas procesan imágenes capturadas por cámaras industriales para identificar defectos, verificar montajes correctos o clasificar piezas con precisiones que superan consistentemente el 99.5% incluso en condiciones variables de iluminación, orientación o presentación.
Las arquitecturas CNN modernas como EfficientNet-B4 o ResNet-50 se optimizan para implementación embebida en controladores robóticos mediante técnicas de cuantización y poda que reducen requisitos computacionales manteniendo precisión diagnóstica. La inferencia en tiempo real se ejecuta en unidades GPU industriales con capacidad para procesar 120 fotogramas por segundo a resoluciones de 1920×1200 píxeles, permitiendo inspección continua en líneas de alta velocidad.
Un aspecto particularmente valioso es la capacidad de estos sistemas para detectar anomalías no categorizadas previamente mediante arquitecturas de auto-codificadores variacionales que modelan la distribución estadística de piezas conformes. Esta detección de novedad permite identificar defectos emergentes antes de que generen problemas de calidad sistémicos, habilitando mantenimiento predictivo y mejora continua automatizada.
Algoritmos genéticos en planificación de rutas robotizadas
Los algoritmos genéticos proporcionan soluciones robustas para problemas de optimización combinatoria en planificación de rutas robotizadas, especialmente en entornos dinámicos con múltiples restricciones. Estas técnicas bio-inspiradas mantienen poblaciones de posibles soluciones que evolucionan mediante operadores de selección, cruzamiento y mutación para explorar eficientemente espacios de búsqueda extremadamente amplios.
En aplicaciones de paletizado multiproducto, los algoritmos genéticos optimizan secuencias de recogida y colocación considerando simultáneamente minimización de distancia recorrida, equilibrio de carga, limitaciones de altura y restricciones de estabilidad. Implementaciones industriales demuestran mejoras del 28% en eficiencia comparado con heurísticas greedy tradicionales, manteniendo tiempos de cómputo compatibles con planificación en tiempo real.
Las variantes más avanzadas implementan codificación cromosómica adaptativa y operadores especializados que incorporan conocimiento específico del dominio. Estas optimizaciones permiten convergencia en menos de 50 generaciones incluso para problemas con espacios de búsqueda superiores a 10^20 posibles soluciones, haciendo viable la replanificación dinámica ante eventos imprevistos como cambios en la secuencia de producción o indisponibilidad temporal de recursos.
Edge computing con NVIDIA jetson para procesamiento en tiempo real
La arquitectura NVIDIA Jetson ha transformado las capacidades de procesamiento embebido en sistemas robóticos industriales, permitiendo ejecutar algoritmos de IA complejos directamente en el borde (edge) sin depender de conectividad cloud. Estas plataformas integran GPUs optimizadas para inferencia de redes neuronales profundas, procesadores multicore ARM y aceleradores dedicados para visión computacional, proporcionando hasta 275 TOPS (Tera Operaciones Por Segundo) en configuraciones Jetson AGX Orin.
La implementación de edge computing en robótica industrial reduce latencias críticas a menos de 10 ms, un orden de magnitud menor que soluciones basadas en cloud, factor determinante en aplicaciones como pick-and-place de alta velocidad donde cada milisegundo impacta directamente en el rendimiento productivo. Adicionalmente, el procesamiento local garantiza continuidad operativa incluso ante interrupciones de conectividad y refuerza seguridad al minimizar transmisión de datos sensibles.
Frameworks optimizados como NVIDIA DeepStream y TensorRT maximizan el rendimiento mediante paralelización, fusión de capas y precisión mixta, permitiendo ejecutar simultáneamente múltiples modelos de IA para diferentes tareas: detección de objetos, segmentación semántica, estimación de pose y predicción de movimiento. Esta capacidad habilitá funcionalidades avanzadas como manipulación guiada por visión con realimentación visual de lazo cerrado a 60 Hz.